Save Time and Money with Effective Packaging Machine Repair Services
Save Time and Money with Effective Packaging Machine Repair Services
Blog Article
Quick and Reliable Packaging Equipment Fixing Solutions to Reduce Downtime
In the competitive landscape of manufacturing, the performance of packaging operations pivots on the dependability of machinery. Quick and dependable repair solutions are important in mitigating downtime, which can result in considerable monetary losses and functional obstacles. Understanding the relevance of timely treatments and the function of specialist service technicians can transform just how companies come close to repair and maintenance. Nevertheless, browsing the myriad options available for repair work services can be tough. What variables should companies think about to guarantee they are making the right selection for their operational requirements?
Relevance of Timely Fixes
Prompt repair work of product packaging machines are important for keeping functional effectiveness and lessening downtime. In the fast-paced environment of manufacturing and packaging, also small malfunctions can cause significant hold-ups and productivity losses. Attending to issues promptly makes sure that equipments run at their optimum capacity, thus safeguarding the flow of operations.
Furthermore, timely and regular upkeep can protect against the rise of minor issues right into major break downs, which often incur greater fixing prices and longer downtimes. A proactive technique to equipment repair not just protects the integrity of the equipment however additionally boosts the total reliability of the production line.
Additionally, timely repair services contribute to the long life of product packaging machinery. Makers that are serviced promptly are less most likely to struggle with too much wear and tear, enabling organizations to optimize their investments. This is specifically important in markets where high-speed product packaging is vital, as the requirement for constant efficiency is critical.
Advantages of Reliable Company
Reputable service carriers play a pivotal duty in making certain the smooth operation of packaging devices. Their experience not only improves the efficiency of repair services but additionally contributes substantially to the long life of equipment.

Additionally, a reputable company uses detailed assistance, including training and advice for staff on device operation and upkeep finest methods. This not only empowers employees however likewise grows a culture of security and performance within the company. On the whole, the benefits of engaging dependable service carriers extend past prompt repairs, favorably influencing the whole operational operations of packaging processes.
Typical Product Packaging Equipment Concerns
In the world of product packaging operations, different concerns can endanger the performance and functionality of devices (packaging machine repair). An additional common concern is imbalance, which can trigger jams and unequal packaging, impacting item high quality and throughput.
Electric issues can also disrupt packaging procedures. Damaged circuitry or malfunctioning sensors might cause erratic device actions, have a peek at this website causing hold-ups and increased functional prices. Furthermore, software application problems can impede the device's programs, resulting in functional ineffectiveness.
Inconsistent item circulation is another vital issue. This can emerge from variants in product form, weight, or dimension, which may impact the device's ability to deal with products precisely. Not enough training of operators can worsen these problems, as inexperienced personnel may not recognize early indicators of breakdown or might abuse the tools.
Resolving these usual product packaging device concerns promptly is necessary to keeping productivity and making certain a smooth operation. Regular inspections and aggressive maintenance can substantially mitigate these issues, promoting a reliable product packaging environment.
Tips for Minimizing Downtime
To reduce downtime in packaging procedures, applying an aggressive upkeep method is crucial. Regularly arranged maintenance checks can identify possible concerns prior to they rise, making official source certain devices operate effectively. Establishing a regimen that consists of lubrication, calibration, and examination of critical elements can dramatically decrease the frequency of unexpected failures.
Training staff to operate machinery correctly and acknowledge early warning indicators of breakdown can also play an essential duty. Equipping operators with the knowledge to carry out basic troubleshooting can prevent minor problems from creating major delays. Maintaining an efficient inventory of necessary extra parts can accelerate repairs, as waiting for components can lead to extended downtime.
Furthermore, recording machine performance and maintenance tasks can aid identify patterns and frequent troubles, permitting targeted interventions. Integrating innovative monitoring technologies can offer real-time information, making it possible for anticipating upkeep and minimizing the risk of unexpected failures.
Finally, cultivating open interaction in between drivers and upkeep groups ensures that any irregularities are quickly reported and dealt with. By taking these positive procedures, services can boost functional performance and dramatically lower downtime in product packaging procedures.
Picking the Right Fixing Solution
Picking the proper repair solution for packaging machines is an essential decision that can significantly affect operational effectiveness. Begin by examining the supplier's experience with your specific kind of packaging tools.
Next, consider the solution provider's online reputation. Seeking responses from other organizations within your market can give insights right into reliability and high quality. Certifications and partnerships with recognized devices manufacturers can likewise show a commitment to quality.
In addition, evaluate their feedback time and availability. A solution company that can use punctual assistance reduces downtime and maintains manufacturing flow stable. It's additionally essential to ask concerning warranty and service assurances, which can mirror the self-confidence the service provider has in their job.

Conclusion
In conclusion, the relevance of trusted and fast packaging maker fixing services can not be overstated, as they play a vital duty in reducing downtime and making sure functional performance. Implementing proactive maintenance methods and spending in team training more enhances the longevity of packaging machinery.
Timely repair services of product packaging equipments are critical for maintaining operational effectiveness and minimizing downtime.Additionally, prompt repair work add to the long life of product packaging machinery. In general, the benefits of involving reputable solution suppliers prolong past prompt repairs, positively affecting the entire operational workflow right here of packaging processes.
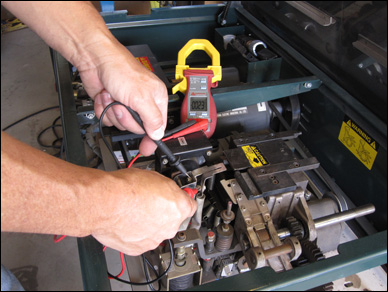
Report this page